UNITY HOMES IS BUILDING WITH THE FUTURE IN MIND.
Alexis Abramson and Chris Sklarin chose Walpole-based Unity Homes, which specializes in energy-efficient, pre-designed and pre-engineered home building.AS THE DEAN of the Thayer School of Engineering at Dartmouth College and a mechanical engineering professor, Alexis Abramson is an expert in building energyefficiency. So, when she and her spouse, Chris Sklarin, decided to build a new home in Hanover, their decision to hire Unity Homes in Walpole was significant.
That’s because Unity isn’t your father’s, or your grandfather’s, homebuilder.
Unlike most traditional homebuilders, Unity employs off-site construction methods— primarily prefabricating panels such as floors, walls and roofs used to create a structure’s envelope, as well as timber work—to build high-performance homes, says Andrew Dey, the company’s director of operations. That fabrication takes place at Unity’s 110,000-square-foot production facility in Keene.
“Most builders are still constructing homes piece-by-piece on the job site, the way homes have been built for the past 200 years,” Dey says. “Building large components in a shop and then assembling them quickly on-site allows for greater control over the process, and much more predictability in the quality, cost and schedule.
“The quality control and precision afforded by our off-site methods are critical for achieving the high standards we’ve set for energy-efficiency, healthy indoor air quality, comfort, sustainability and durability,” he says.
Unity Homes spun off from the Walpole-based Bensonwood Homes in 2012 after a number of Bensonwood employees “were interested in finding ways to bring that high quality to more people by figuring out ways to lower the costs,” says Dey, who worked at Bensonwood for 13 years before joining Unity. In the late 1900s and early 2000s, Bensonwood had gained a solid reputation in the field for building highend timber-frame homes.
“We made several attempts within Bensonwood to develop a line of houses that would be more like products— predesigned and pre-engineered—but they never gained traction,” Dey says. “Eventually, we realized that to succeed in lowering costs, we’d have to start a new company with its own mission, marketing and process.”
Unity employees refer to the company as a “40-year-old startup,” a nod to Bensonwood’s prior 40 years of experience. Unity’s stated mission, according to its website, “is to improve the lives of our clients, our partners and our team members by building homes that are high performance, low energy and minimal impact. By doing this using innovative off-site construction methods and prefabricated components, we provide the housing industry with a new paradigm for home building—a ‘Better Way to Build.’” To achieve that mission, Unity is guided by the following core values that homes should: promote health, comfort and peace of mind; be built using sustainable materials and processes; use minimal energy, and be net-zero ready; be adaptable to changing needs over time; be designed and built through processes that are streamlined and minimize waste; and be built with the impact on future generations in mind.
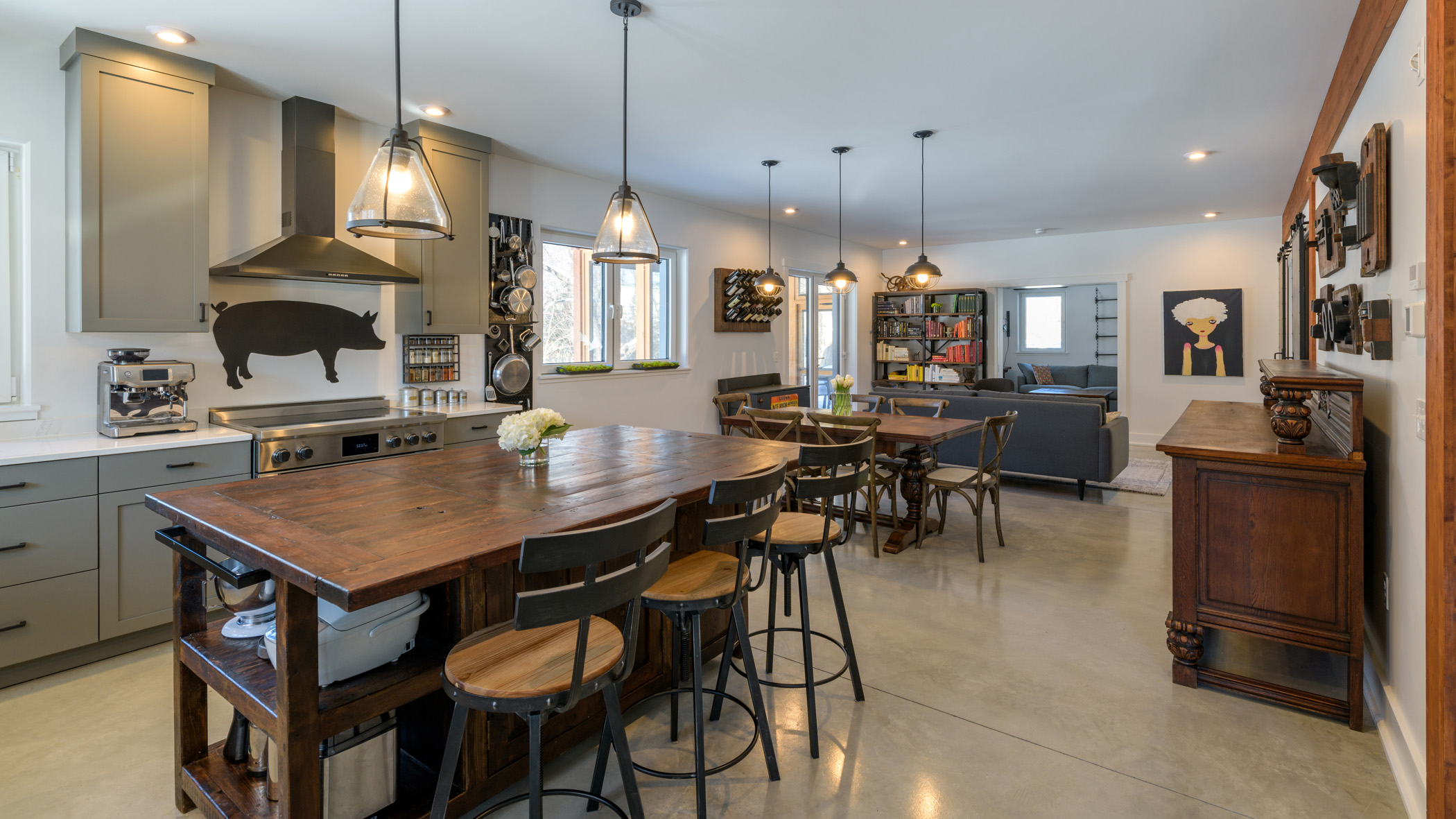
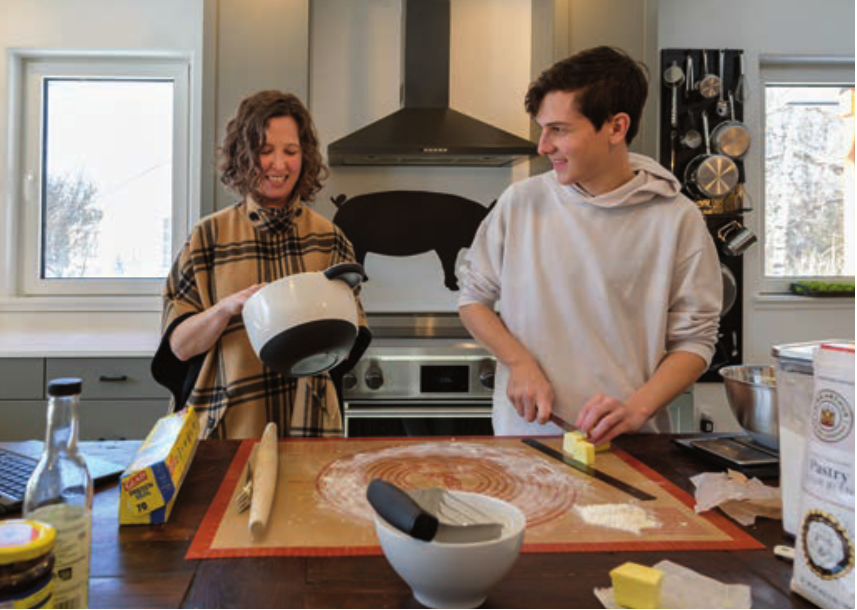
Right: The 2,651-square-foot, two-story house includes a large, open-concept first floor.
Right, below: Homeowners Alexis Abramson and Chris Sklarin
That combination of benefits was an undeniable lure for Abramson and Sklarin when they began their search for a new home for themselves and their children Robin, 19, now a sophomore at Oberlin College in Ohio, and Wyatt, 17, a junior at Hanover High School.
A tight housing market, and a dearth of move-in-ready homes, welcomed the couple when they moved from Ohio to New Hampshire.
“We were looking for a home close to the Dartmouth campus and Hanover High School. But few houses were on the market, and those that were needed a considerable amount of renovation,” Abramson says. “Chris and I had always talked about building an energy-efficient home and started exploring options. I learned that Dartmouth had hired Unity to construct four houses in town, and we spoke with them and a couple of other companies regarding the possibility.
“Unity seemed to align best—high-quality construction, a priority for energy-efficiency and an ability to be semicustom all pointed to Unity being the best fit,” Abramson says. “Our Realtor found someone in town who was looking to sell a small home just behind the high school and a stone’s throw from town. We jumped at the opportunity.”
“They looked at a number of existing homes, but none were very well built, and they all needed work,” Dey says. “Alexis and Chris had heard plenty of stories about gut renovations that turned into nightmares. They concluded that they would have to build a new home.
“At the top of Alexis and Chris’s list of criteria for their new home was that it be a walkable distance to the high school that their kids would be attending,” he says. “Their second priority was energy-efficiency. As dean of the Thayer School and a mechanical engineer herself, Alexis felt strongly that she and her family should ‘walk the talk.’” The couple signed a design contract with Unity in March 2020, selecting the company’s Värm design, which is one of five “flexible, expandable platforms” offered by Unity.
The Värm is a Colonial-style design (two stories, with between three and four bedrooms, between 2 and 3 1/2 baths, from 1,520 and 2,940 square feet, with a starting price of $365,000). Its name comes from Värmland, a province in middle Sweden where Unity founder Tedd Benson has family roots; the simple gable form is inspired by a typical Swedish countryside home.
Other platforms include the Tradd, a “tall Cape” (two stories, with between two and five bedrooms, 1 1/2 to 3 1/2 baths, from 2,064 and 2,770 square feet, and a starting price of $425,000); the Xyla bungalow (single story, with between two and three bedrooms, one to two baths, from 1,032 and 1,820 square feet, starting at $265,000); the Zum contemporary (single story, with between one and four bedrooms, one to two baths, from 1,060 and 1,970 square feet, starting at $305,000); and the Nano cottage (with one or two stories, between 480 and 960 square feet, starting at $85,000).
“Unity offered three approaches to engagement during the design phase,” Abramson says. “We chose the middle one, which was essentially a semi-custom approach, which allowed us to move some things around within reason.
“Unity has set layouts that can be customized to some extent within their constraints,” she says. “For example, we chose to have two bathrooms on the second floor instead of a bathroom and laundry room. And, we changed the dimensions of the screened-in porch to fit on our plot of land.”
Unity provided the couple with a catalog, allowing Abramson and Sklarin to choose features such as the exterior paneling, roofing, window details, plumbing fixtures, flooring and the like. They went “off book” for items like lighting, shower doors, the kitchen island and bathroom vanities (Abramson wanted to have the latter two items custommade from reclaimed wood). Dey says Unity welcomes that kind of input.
“In terms of the design process, Alexis had plenty of input early on,” he says. “In fact, because our design/build process is based in 3D modeling that provides the instructions for the computer-controlled machines in our shops, virtually all the main design decisions need to be made before construction begins. We work hard to ensure our clients have the information needed to make good decisions, because making changes during the construction process can be difficult and costly.”
That approach reflects one of Unity’s primary strategies to reducing costs, which is to “generate all of our designs from a system we’ve developed that’s optimized for our manufacturing process and the performance of the homes,” Dey says.
“Most of our clients appreciate having some wiggle room during the design process, but also not having to start from a blank slate.”
Clients, he says, would rather choose from a menu of timetested options provided by Unity.
Abramson and Sklarin felt that the farmhouse-look of Unity Homes’ Värm design would blend well with the neighborhood.
“If the constraints in our process are not going to meet the needs of a prospective client, we try to identify that early in the process and point them toward a company—possibly Bensonwood or perhaps an independent architect—who could better serve their needs,” Dey says.
Given her mechanical-engineering background, Abramson says she also “inserted myself into the heating and cooling system design, and we ended up with a system a bit different from what was originally proposed.”
The smaller, single compressor/condenser unit has three cassettes (out of which conditioned air is blown) in three locations in the home.
“Rather than putting individual units in each bedroom, we use transfer fans and the ventilation system to circulate the conditioned air to reach other areas,” she says. “On the first floor, we installed radiant, electric wall panels in far-to-reach locations—rather than conventional electric baseboards—to provide heat on only the coldest days of the winter.”
Once the final designs were drawn up, the existing small house on the lot was removed and construction of the new home began—despite the pandemic. Installation of the foundation installation began in July, while Unity craftsmen were prefabricating the panels in the Keene shop. The shell of the house was assembled in August.
“I can say from Unity’s perspective that working on such a tight ‘infill’ lot was challenging, because we had little space for staging equipment, storing panel bundles, setting the crane, etc.,” Dey says. “But we managed.”
Although Dey says he had hoped to have the Abramson- Sklarin family settled into their new home by Christmas 2020, “construction was significantly disrupted by the pandemic.”
“We were proud to be able to hand over the keys to Alexis and Chris in January 2021,” Dey says. “While it’s true that working with Unity can result in an accelerated construction schedule, the pandemic has wreaked havoc with many aspects of the homebuilding business. Despite our diligent efforts to adjust and adapt to ever-changing conditions, our lead time is currently longer than we’d like it to be.”
Flexibility in the Värm layout was another key reason why the couple chose that design. For instance, they chose to have two bathrooms on the second floor instead of a bathroom and laundry room. They selected plumbing details, flooring and other features from Unity Homes’ catalog, and went “off book” for things like lighting, shower doors and bathroom vanities.
If Abramson and Sklarin were disappointed with the delay, you wouldn’t know it.
“We’re happy with the finished product,” Abramson says.
“In hindsight, there are few things I would change, such as adding an extra room for the teenagers to hang out in when the parents are home. We chose not to put in a basement—in our experience, nothing good ever happens in a basement— and so we’re missing that extra room.
“We designed the house pre-COVID, thinking fewer people would be inhabiting it most of the time than actually are,” she says. “Additionally, we probably would have thought more about how to integrate sufficient desk/office space into the house if we had known that remote work/school would become more prevalent.”
The 2,651-square-foot, two-story house includes a large, open-concept first floor with the kitchen, dining room, living room, home office, family room that can be used as a master bedroom, three bedrooms, three full bathrooms, one half-bathroom, mudroom that doubles as a laundry room, 252 square feet in porch space (including a screenedin porch), and 581-square-foot, two-car garage with storage space above.
“We felt the exterior design—more of a farmhouselook than the other [options]—would blend well with the neighborhood, which was important since we’re in a more suburban setting,” Abramson says. “The various options for the layout also made the design attractive. The house is on a relatively small and flat plot of land, and we used nearly every inch we could within zoning constraints to build on.”
When asked to name her favorite aspect of her home, Abramson says: “The open layout is fantastic. I love being able to gather essentially in one room, including the kitchen, and be together either as a family or with others, too.
“We’re big foodies, and having a great kitchen equipped with everything we need in easy-to-access places is key,” she says. “I have fallen in love with my induction range on which I can boil a large pot of water in minutes and have precise control over heating on the stove or in the oven.”
The couple opted for pocket doors in various places throughout the house, which helps the rooms flow into each other without doors getting in the way (but provides privacy when needed). Abramson says she also loves the tilt-andturn European-style windows.
“The screened-in porch, while small, is a wonderful place to have coffee in the morning,” she says. “We added directional radiant heaters to take the chill off on cold days and enable outdoor, cold-weather gathering during COVID times. And although the bedrooms are small, I do enjoy being in bed with the window shades open—motorized and operational from a remote—feeling like I’m living in the trees.”
Dey says the most admirable quality of Unity homes is “how lightly they live on the planet,” combing beauty and durability “to help ensure they’ll still be occupied in a hundred years.”
“My favorite aspect that’s unique to this house is the furniture or maybe you could say the interior decorating,” he says. “I think Alexis referred to the mix of old and new as ‘industrial vintage.’ It’s a reflection of her creativity and gives the home a very distinctive feeling.”
The all-electric structure is also designated as an Energy Star home (highly insulated, airtight home), featuring high R-value floors, walls and roof; airtight construction; low heating and cooling loads that result from a well-insulated building envelope; efficient appliances (including an airsource heat pump for heating and cooling, heat-pump water heater, and electric induction ranges); a heat-recovery ventilation system that ensures a continuous supply of filtered fresh air; and the aforementioned triple-glaze, double-gasket windows. Abramson says she expects solar panels to be installed this spring, which will help the couple achieve net-zero performance (meaning the house produces as much energy as it uses).
“Today, on the coldest day of the winter, we are very comfortable while our energy-efficient, cold-climate heat pump cranks away,” she says in mid-January.
Dey says, “It’s hard to measure how important these elements are to our clients,” but adds that these features factor significantly in clients’ choices to work with Unity.
“For some clients, these considerations are paramount,” he says. “Regardless of how our clients respond to the features, they’re universally appreciative of the benefits—low utility bills, consistently comfortable interior temperatures, air quality that just feels good, and the less-tangible but real feeling that comes from knowing that the choices they’ve made for their new home are, in some small way, helping to minimize their impact on the planet and preserve it for future generations.”
For Abramson and Sklarin, Unity’s approach goes far beyond a marketing script.
“Factory-built homes—either panels that comprise the envelope or fully outfitted modules placed on-site—are absolutely the future of home building,” Abramson says. “The construction industry has not seen much gain in productivity in decades, particularly compared to other sectors.
“With labor shortages in the building industry, rising construction costs and the need to build ‘greener’ homes, we must find ways to enhance productivity, integrate energyefficiency and reduce timelines to build,” she says. “Unity is doing just that.”
RESOURCES
Bensonwood • (603) 756-3600 • bensonwood.com
Unity Homes • (603) 756-3600 • unityhomes.com